VIP member
Solvent oil flowmeter, toluene pipeline flowmeter
Solvent oil flowmeter, toluene pipeline flowmeter
Product details
LWGY seriesSolvent oil flowmeterThe sensor (hereinafter referred to as the sensor) is based on the principle of torque balance and belongs to the velocity flow meter. Sensors have the characteristics of simple structure, lightweight, high accuracy, good reproducibility, sensitive response, and easy installation, maintenance, and use. They are widely used in industries such as petroleum, chemical, metallurgical, water supply, and papermaking, and are ideal instruments for flow measurement and energy conservation.
Sensors and display instruments are used in conjunction, suitable for measuring liquids in closed pipelines that do not corrode stainless steel 1Cr18Ni9Ti, 2Cr13, corundum Al2O3, hard alloys, and have no impurities such as fibers or particles. If matched with display instruments with special functions, quantitative control, over limit alarm, etc. can also be performed. The explosion-proof type (ExmIIT6) of this product can be used in environments with explosive hazards.
The sensor is suitable for media with viscosity less than 5 × 10-6m2/s at operating temperature. For liquids with viscosity greater than 5 × 10-6m2/s, the sensor needs to be calibrated with real liquid before use.
If users require special forms of sensors, they can negotiate to place an order. If explosion-proof sensors are needed, they should be explained in the order.

(1)structure characteristics
The sensor is a hard alloy bearing thrust type, which not only ensures accuracy and improves wear resistance, but also has the characteristics of simple structure, firmness, and easy disassembly and assembly.
(2)Working principle
The fluid flows through the sensor housing. Due to the angle between the blades of the impeller and the flow direction, the impulse of the fluid causes the blades to have a rotational torque. After overcoming the friction torque and fluid resistance, the blades rotate. After the torque is balanced, the speed stabilizes. Under certain conditions, the speed is proportional to the flow rate. Due to the magnetic conductivity of the blades, they are in the magnetic field of the signal detector (composed of permanent magnet and coil). The rotating blades cut the magnetic field lines and periodically change the magnetic flux of the coil, causing electrical pulse signals to be induced at both ends of the coil. This signal is amplified and shaped by the amplifier, forming a continuous rectangular pulse wave with a certain amplitude, which can be transmitted to the display instrument remotely to display the instantaneous flow rate or total amount of the fluid. Within a certain flow range, the pulse frequency f is proportional to the instantaneous flow rate Q of the fluid flowing through the sensor, and the flow equation is:
In the formula:
F - Pulse frequency [Hz]
K - the instrument coefficient of the sensor [1/m3], given by the calibration sheet. If [1/L] is used as the unit
Q - Instantaneous flow rate of fluid (under working conditions) [m3/h]
3600- Conversion factor
The instrument coefficient of each sensor is filled in the calibration certificate by the manufacturer, and the k value is set in the matching display instrument to display the instantaneous flow rate and cumulative total amount.
2Basic parameters and technical performance of solvent oil flowmeter
(1)Basic parameters:See Table 1
TABLE I
Sensors with diameters ranging from DN4 to DN40 are threaded connections, with a maximum working pressure of 6.3 MPa;
DN50-DN200 caliber sensors are flange connected, with a maximum working pressure of 2.5Mpa;
Sensors with diameters ranging from DN4 to DN10 are equipped with front and rear straight pipe sections and filters.
Our company can provide front and rear straight pipe sections for sensors with a diameter of DN15 or above.
(2)Medium temperature:-20~+120℃.
(3)ambient temperature:- 20~+55℃.
(4)Power supply:Voltage: 12V ± 10%, Current: ≤ 10mA.
(5)Output voltage amplitude:High level ≥ 8V, low level ≤ 0.8V
(6)Transmission distance:The distance from the sensor to the display instrument can reach 1000m
⑵ Use and adjustment of solvent oil flowmeter
When using, the tested liquid should be kept clean and free of impurities such as fibers and particles.
At the beginning of use, the sensor should be slowly filled with liquid before opening the outlet valve,
It is strictly prohibited for the sensor to be impacted by high-speed fluid when it is in a liquid free state.
The maintenance cycle of sensors is generally six months. During maintenance and cleaning, please be careful not to damage the parts inside the measuring chamber
Don't be the impeller. Please pay attention to the position relationship between the guide components and the impeller during assembly.
When the sensor is not in use, the internal liquid should be cleaned and protective covers should be added at both ends of the sensor to prevent dust and dirt from entering,
Then store it in a dry place.
◆ The filter used should be cleaned regularly. When not in use, the liquid inside should be cleaned. Like the sensor, it should be sealed with a dust boot and stored in a dry place.
The transmission cable of the sensor can be laid overhead or buried underground (iron pipes should be covered when buried underground)
Before installing the sensor, connect the wires to the display instrument or oscilloscope, turn on the power, blow or manually turn the impeller to quickly rotate and observe if there is any display. When there is a display, install the sensor. If there is no display, check the relevant parts and eliminate the fault.
4、 Solvent oil flowmeter
The LWY turbine flowmeter is based on the LWGY modelSolvent oil flowmeterOn the basis of this, 24VDC power supply and 4-20mA two-wire current transmission function have been added, which is particularly suitable for use with computer control systems such as display instruments, industrial computers, DCS, etc.
It has both on-site display and remote transmission output functions.
The operation method for setting instrument coefficients refers to "IV. LWY typeSolvent oil flowmeter”The differences in the explanation of the numerical part are as follows:
The parameters of the instrument have been adjusted before leaving the factory, and generally do not need to be adjusted again.
If under normal conditions of use, it is found that some points of the output remote current are out of tolerance compared with the theoretical value, adjust the adjustable resistance on the circuit board as follows: open the front case of the instrument, take out the circuit board, and there are two adjustable resistors on the bottom layer of the circuit board, of which the adjustment W3 (202) can adjust 4mA, and the adjustment W4 (502) can adjust 20mA. Note that the adjustment range should not be too large. Install it as it is after adjustment.
Instrument structure editing
1. The instrument installation adopts flange connection, threaded connection and clamping type;
2. The direction of liquid flow during installation should be consistent with the direction indicated by the arrow on the sensor housing, and the upstream straight pipe section should be ≥ 6DS, and the downstream straight pipe section should be ≥ 5DS (DS is the measured inner diameter of the tested pipeline).
3. Sensors should be kept away from external magnetic fields. If unavoidable, necessary measures should be taken;
4. In order to avoid affecting the normal transportation of liquids during maintenance, bypass pipelines should be installed outside the straight pipe sections at both ends of the sensor (as shown in Figure 4);
5. When installing sensors outdoors, please ensure that the amplifier plug is waterproofed;
6. The wiring of sensors and display instruments should be selected according to the power supply of the amplifier. Please refer to the relevant "user manual" for details.
Install and use editing
install
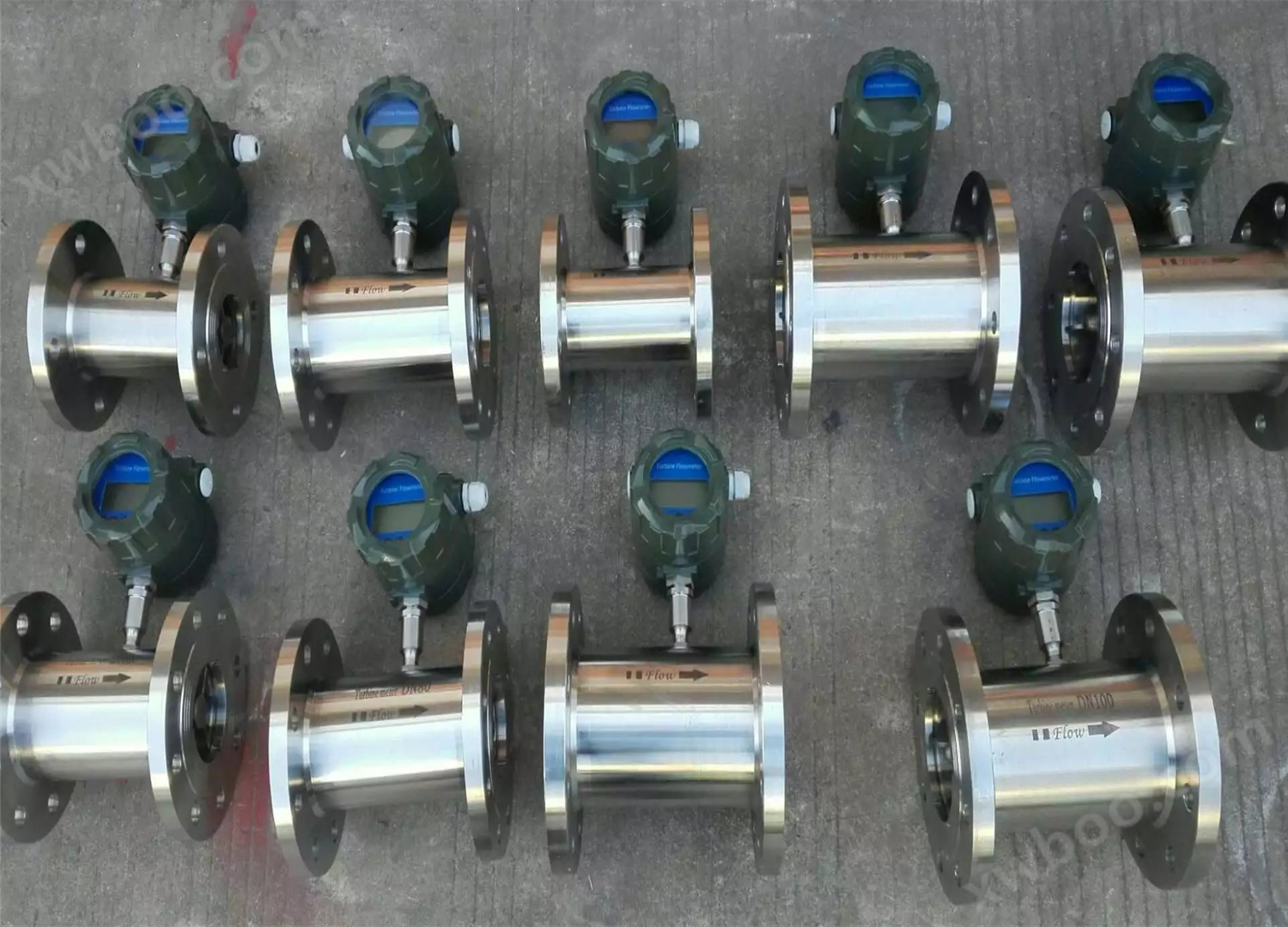
1. Compression ring 2. Bolt 4 × 14 3. Gasket 4. Sealing gasket 5. Steel wire 1Cr18Ni9Ti-0.8 × 2.5 6. Filter screen 7. Seat
Filter structure diagram
Figure 1 Schematic diagram of LWGY-4-10 sensor structure and installation dimensions
1. Shell 2. Front guide piece 3. Impeller 4. Rear guide piece 5. Pre amplifier
Figure 2 Schematic diagram of LWGY-15-40 sensor structure and installation dimensions
1. Ball bearing 2. Front guide component 3. Expansion ring 4. Shell 5. Pre amplifier 6. Impeller 7. Bearing 8. Shaft
Figure 3 Schematic diagram of LWGY-50-200 sensor structure and installation dimensions
Figure 4 Schematic diagram of sensor and display instrument wiring
Table 2
Sensors can be installed horizontally or vertically, and the fluid direction must be upward when installed vertically. The liquid should fill the pipeline without any bubbles. During installation, the direction of liquid flow should be consistent with the direction indicated by the arrow on the sensor housing. The upstream end of the sensor should have a straight pipe section at least 20 times the nominal diameter, and the downstream end should have a straight pipe section at least 5 times the nominal diameter. The inner wall should be smooth and clean, without defects such as dents, scale, and peeling. The axis of the sensor's pipeline should be aligned with the axis of the adjacent pipeline, and the gasket used for connecting and sealing should not penetrate deep into the interior of the pipeline.
Sensors should be kept away from external electric and magnetic fields, and effective shielding measures should be taken if necessary to avoid external interference.
In order to avoid affecting the normal transportation of liquids during maintenance, it is recommended to install a bypass pipeline at the installation location of the sensor.
Design schematic diagram of installation side pipeline
Design schematic diagram of installation side pipeline
When installing sensors outdoors, please ensure that the amplifier and plug are waterproofed. The wiring between the sensor and the display instrument is shown in Figure 4.
When there are impurities in the fluid, a filter should be installed, and the mesh size of the filter should be determined according to the flow rate of impurities, generally ranging from 20 to 60 mesh. When there is free gas mixed in the fluid, a deaerator should be installed. The entire pipeline system should be well sealed. Schematic diagram of bypass pipeline
Users should fully understand the corrosion situation of the tested medium and strictly prevent the sensor from being corroded.
Sensors and display instruments are used in conjunction, suitable for measuring liquids in closed pipelines that do not corrode stainless steel 1Cr18Ni9Ti, 2Cr13, corundum Al2O3, hard alloys, and have no impurities such as fibers or particles. If matched with display instruments with special functions, quantitative control, over limit alarm, etc. can also be performed. The explosion-proof type (ExmIIT6) of this product can be used in environments with explosive hazards.
The sensor is suitable for media with viscosity less than 5 × 10-6m2/s at operating temperature. For liquids with viscosity greater than 5 × 10-6m2/s, the sensor needs to be calibrated with real liquid before use.
If users require special forms of sensors, they can negotiate to place an order. If explosion-proof sensors are needed, they should be explained in the order.

(1)structure characteristics
The sensor is a hard alloy bearing thrust type, which not only ensures accuracy and improves wear resistance, but also has the characteristics of simple structure, firmness, and easy disassembly and assembly.
(2)Working principle
The fluid flows through the sensor housing. Due to the angle between the blades of the impeller and the flow direction, the impulse of the fluid causes the blades to have a rotational torque. After overcoming the friction torque and fluid resistance, the blades rotate. After the torque is balanced, the speed stabilizes. Under certain conditions, the speed is proportional to the flow rate. Due to the magnetic conductivity of the blades, they are in the magnetic field of the signal detector (composed of permanent magnet and coil). The rotating blades cut the magnetic field lines and periodically change the magnetic flux of the coil, causing electrical pulse signals to be induced at both ends of the coil. This signal is amplified and shaped by the amplifier, forming a continuous rectangular pulse wave with a certain amplitude, which can be transmitted to the display instrument remotely to display the instantaneous flow rate or total amount of the fluid. Within a certain flow range, the pulse frequency f is proportional to the instantaneous flow rate Q of the fluid flowing through the sensor, and the flow equation is:
In the formula:
F - Pulse frequency [Hz]
K - the instrument coefficient of the sensor [1/m3], given by the calibration sheet. If [1/L] is used as the unit
Q - Instantaneous flow rate of fluid (under working conditions) [m3/h]
3600- Conversion factor
The instrument coefficient of each sensor is filled in the calibration certificate by the manufacturer, and the k value is set in the matching display instrument to display the instantaneous flow rate and cumulative total amount.
2Basic parameters and technical performance of solvent oil flowmeter
(1)Basic parameters:See Table 1
TABLE I
Sensors with diameters ranging from DN4 to DN40 are threaded connections, with a maximum working pressure of 6.3 MPa;
DN50-DN200 caliber sensors are flange connected, with a maximum working pressure of 2.5Mpa;
Sensors with diameters ranging from DN4 to DN10 are equipped with front and rear straight pipe sections and filters.
Our company can provide front and rear straight pipe sections for sensors with a diameter of DN15 or above.
(2)Medium temperature:-20~+120℃.
(3)ambient temperature:- 20~+55℃.
(4)Power supply:Voltage: 12V ± 10%, Current: ≤ 10mA.
(5)Output voltage amplitude:High level ≥ 8V, low level ≤ 0.8V
(6)Transmission distance:The distance from the sensor to the display instrument can reach 1000m
⑵ Use and adjustment of solvent oil flowmeter
When using, the tested liquid should be kept clean and free of impurities such as fibers and particles.
At the beginning of use, the sensor should be slowly filled with liquid before opening the outlet valve,
It is strictly prohibited for the sensor to be impacted by high-speed fluid when it is in a liquid free state.
The maintenance cycle of sensors is generally six months. During maintenance and cleaning, please be careful not to damage the parts inside the measuring chamber
Don't be the impeller. Please pay attention to the position relationship between the guide components and the impeller during assembly.
When the sensor is not in use, the internal liquid should be cleaned and protective covers should be added at both ends of the sensor to prevent dust and dirt from entering,
Then store it in a dry place.
◆ The filter used should be cleaned regularly. When not in use, the liquid inside should be cleaned. Like the sensor, it should be sealed with a dust boot and stored in a dry place.
The transmission cable of the sensor can be laid overhead or buried underground (iron pipes should be covered when buried underground)
Before installing the sensor, connect the wires to the display instrument or oscilloscope, turn on the power, blow or manually turn the impeller to quickly rotate and observe if there is any display. When there is a display, install the sensor. If there is no display, check the relevant parts and eliminate the fault.
4、 Solvent oil flowmeter
The LWY turbine flowmeter is based on the LWGY modelSolvent oil flowmeterOn the basis of this, 24VDC power supply and 4-20mA two-wire current transmission function have been added, which is particularly suitable for use with computer control systems such as display instruments, industrial computers, DCS, etc.
It has both on-site display and remote transmission output functions.
The operation method for setting instrument coefficients refers to "IV. LWY typeSolvent oil flowmeter”The differences in the explanation of the numerical part are as follows:
The parameters of the instrument have been adjusted before leaving the factory, and generally do not need to be adjusted again.
If under normal conditions of use, it is found that some points of the output remote current are out of tolerance compared with the theoretical value, adjust the adjustable resistance on the circuit board as follows: open the front case of the instrument, take out the circuit board, and there are two adjustable resistors on the bottom layer of the circuit board, of which the adjustment W3 (202) can adjust 4mA, and the adjustment W4 (502) can adjust 20mA. Note that the adjustment range should not be too large. Install it as it is after adjustment.
Instrument structure editing
1. The instrument installation adopts flange connection, threaded connection and clamping type;
2. The direction of liquid flow during installation should be consistent with the direction indicated by the arrow on the sensor housing, and the upstream straight pipe section should be ≥ 6DS, and the downstream straight pipe section should be ≥ 5DS (DS is the measured inner diameter of the tested pipeline).
3. Sensors should be kept away from external magnetic fields. If unavoidable, necessary measures should be taken;
4. In order to avoid affecting the normal transportation of liquids during maintenance, bypass pipelines should be installed outside the straight pipe sections at both ends of the sensor (as shown in Figure 4);
5. When installing sensors outdoors, please ensure that the amplifier plug is waterproofed;
6. The wiring of sensors and display instruments should be selected according to the power supply of the amplifier. Please refer to the relevant "user manual" for details.
Install and use editing
install
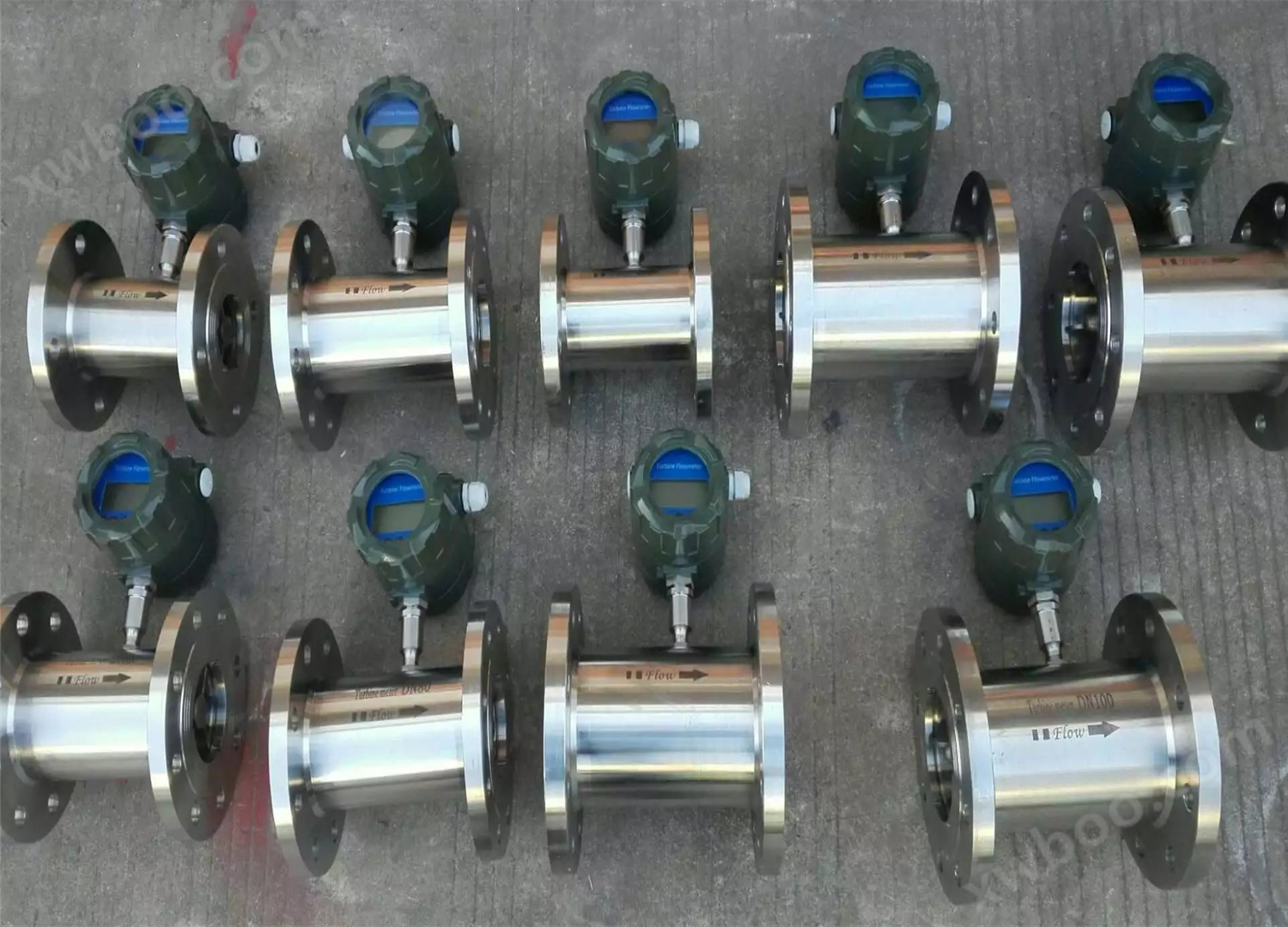
1. Compression ring 2. Bolt 4 × 14 3. Gasket 4. Sealing gasket 5. Steel wire 1Cr18Ni9Ti-0.8 × 2.5 6. Filter screen 7. Seat
Filter structure diagram
Figure 1 Schematic diagram of LWGY-4-10 sensor structure and installation dimensions
1. Shell 2. Front guide piece 3. Impeller 4. Rear guide piece 5. Pre amplifier
Figure 2 Schematic diagram of LWGY-15-40 sensor structure and installation dimensions
1. Ball bearing 2. Front guide component 3. Expansion ring 4. Shell 5. Pre amplifier 6. Impeller 7. Bearing 8. Shaft
Figure 3 Schematic diagram of LWGY-50-200 sensor structure and installation dimensions
Figure 4 Schematic diagram of sensor and display instrument wiring
Table 2
Sensors can be installed horizontally or vertically, and the fluid direction must be upward when installed vertically. The liquid should fill the pipeline without any bubbles. During installation, the direction of liquid flow should be consistent with the direction indicated by the arrow on the sensor housing. The upstream end of the sensor should have a straight pipe section at least 20 times the nominal diameter, and the downstream end should have a straight pipe section at least 5 times the nominal diameter. The inner wall should be smooth and clean, without defects such as dents, scale, and peeling. The axis of the sensor's pipeline should be aligned with the axis of the adjacent pipeline, and the gasket used for connecting and sealing should not penetrate deep into the interior of the pipeline.
Sensors should be kept away from external electric and magnetic fields, and effective shielding measures should be taken if necessary to avoid external interference.
In order to avoid affecting the normal transportation of liquids during maintenance, it is recommended to install a bypass pipeline at the installation location of the sensor.
Design schematic diagram of installation side pipeline
Design schematic diagram of installation side pipeline
When installing sensors outdoors, please ensure that the amplifier and plug are waterproofed. The wiring between the sensor and the display instrument is shown in Figure 4.
When there are impurities in the fluid, a filter should be installed, and the mesh size of the filter should be determined according to the flow rate of impurities, generally ranging from 20 to 60 mesh. When there is free gas mixed in the fluid, a deaerator should be installed. The entire pipeline system should be well sealed. Schematic diagram of bypass pipeline
Users should fully understand the corrosion situation of the tested medium and strictly prevent the sensor from being corroded.
Online inquiry